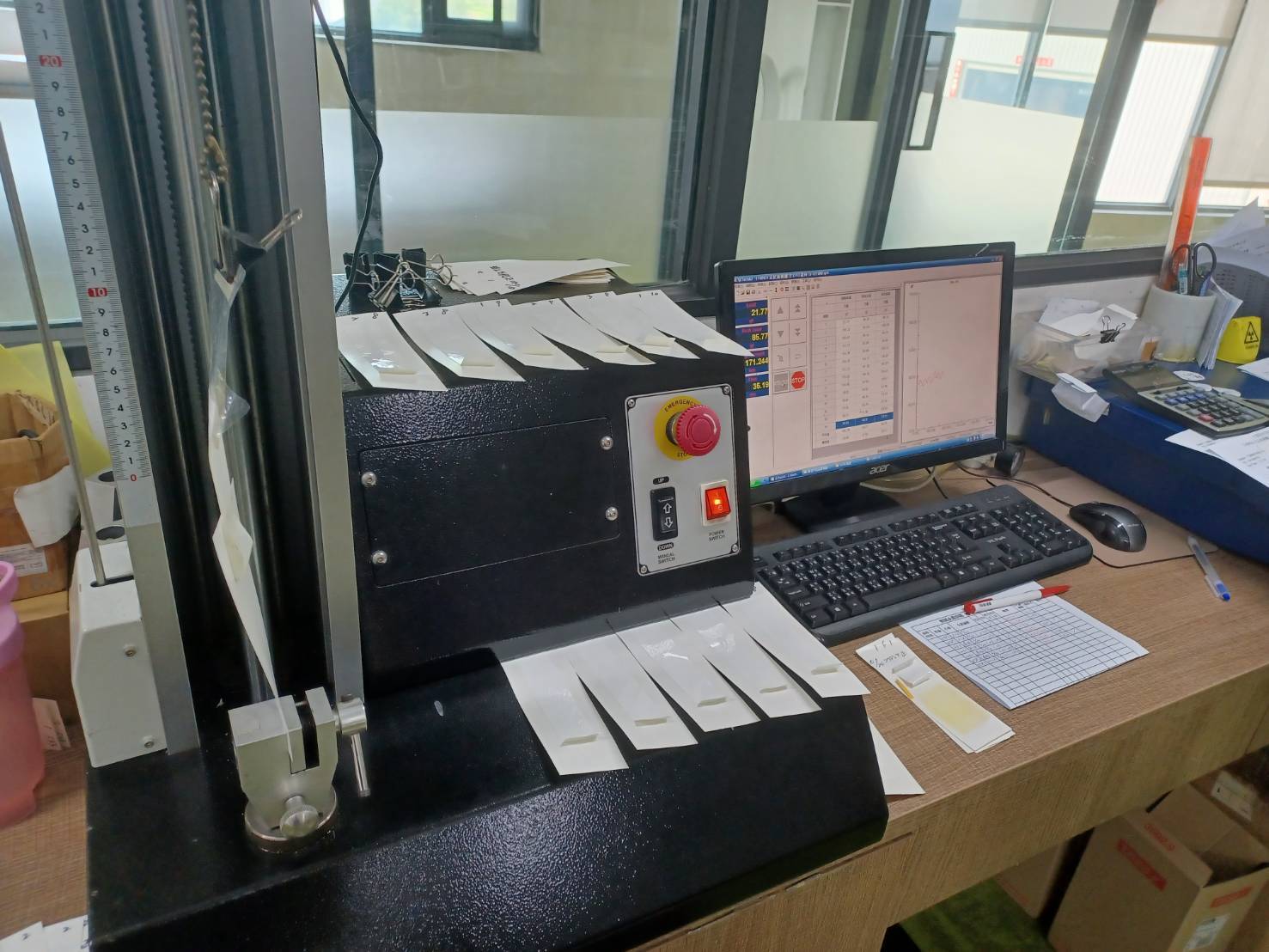
Quality Management
ISO 9001 certified
To ensure product consistency and stability, JPC has introduced precision testing equipment and rigorous inspection procedures. We firmly believe that quality is the core value of our enterprise, so we continuously strive to improve our technology and optimize processes to provide customers with the best solutions. Customer satisfaction is our greatest motivation, and we are dedicated to being a trusted partner for our customers.
As a professional coating plant, we are committed to providing high-quality products. We utilize various coating technologies to produce a wide range of items, including general food products (paper cups, food containers, hamburger paper, steamer paper), labels/tape base paper, and more. These coated papers are developed through precise coating technology platforms, supported by robust quality control policies, appropriate SOP production processes, and comprehensive personnel training. With a monthly production yield of 96.2%, we effectively reduce waste and enhance production efficiency.
In our factory, we rigorously control the quality of raw materials used for producing such as laminating packaging paper, glassine release paper, and CCK release paper. We conduct inspections according to standard procedures and specifications, checking basis weight with electronic balances and thickness with thickness tester. Incoming inspection is the first step in quality management, ensuring control over raw material quality to enhance product yield and production stability.
After finishing the production, we conduct a series of rigorous testing procedures to ensure the highest quality standards.
Firstly, we use an XRF analyzer to inspect the coating weight on the paper surface. This ensures that the coating weight of the release agent is within standard, ensuring stability in release force.
Secondly, we perform aging tensile tests using international inspection standard FINAT10, combined with oven aging. This further quantifies the release force to assess compliance with customer needs and standards.
Lastly, we conduct a dye-test using red ink to examine the coverage of the release agent. This test ensures uniform coverage on the paper surface, preventing issues like partially bad adhesion.
Finally, during packaging, we conduct inspections for appearance, labels, markings, and quantity.
Through these testing procedures, we ensure that each batch of produced paper meets strict quality requirements and provides outstanding performance and usability.
Below is the introduction of the instruments:
- Electronic Balance: used to measure the basis weight of the paper.
- Thickness Tester: utilized to measure the thickness of the paper.
- Tensile Testing Machine: employed according to international standard FINAT10 to measure release force.
- XRF Analyzer: utilized for X-ray detection of coating weight on the paper surface.
- Dye-test: use red ink to check the uniformity of release agent on the paper surface.
- Oven: Using fixed-time heating to simulate aging conditions to observe changes in release force over time.